WE ARE BEST IN SALE& COMMISSIONING&PROGRAMMING OF ROBOTIC UNITS
We are specialist for SALE Robotic Device UNITS
Robots Palletising line TOUBKAL
ARE YOU LOOKING FOR ANY ROBOTS ?
WE GOT FOR YOU ASAP ON REQUEST!
robot programming following wordwide standart
Siemens SIMATICS
ROCKWELL / Allan Bradley / RS Logic
Omron
ABB
Schneider
Alstom
Beckhoff
Delta
Mitsubishi
Modicon
Lenze
Yokogawa
Nordson
Contec
PILZ
Pro-Face
GE - Intelligence Platforms
Festo
Omega
Panasonic
Eaton
Smartscan
Safety PLC
Klockner Moeller
PNOZ Multi Safety PLC
ICS Triplex PLC
Medoc
Phoenix Contact Interbus
System Worx
Intellution FIX DMACS
Honeywell SCAN3000
Panel Builder
IPC
Bosch
Micrologix PLC's
FactoryTalk
SCADA systems
WinCC
Eurotherm
Omega
Fanuc
Ingersoll Rand
Epson
Agilent Technologies
Wonderware Intouch
SCADA
GuardLogix
RSStudio
MING (Mitsubishi Integrated Network Graphics)
ABB S3, S4, S4 (c) / S4 (C plus), IRC5
Comau Smart H4, CG3
Fanuc RH / RJ / RJ2,3
KUKA - KRC Series / KRC1 / KRC2 / KRC4
Kawasaki AD, C, ZX series
Motoman
Applications
VisionTools
Resistance Spot Welding
Materials Handling
Sealing / Gluing
MIG / MAG Welding
Stud Welding and Riveting
BIW / Robotic Paint Systems
Powertrain Assembly
Palletising Robots
Assembly and Sub Systems
- SPS-Qualifizierung Siemens VASS V05
- SPS-Zertifizierung Siemens VASS V05
- VKR C4 Qualifizierung VASS Standard
- VKR C4 Zertifizierung VASS Standard
- VWRS IRC5 Programmieren
- VWRS IRC5 Profinet
- VWRS IRC5 VASS Standard
- VWRS IRC5 VASS Zertifizierung
- Elektroinstallation (Bus- und Netzwerkverkabelung LWL)
- Antriebstechnik SEW
COMAU KUKA ABB FANUC YASKAWA/MOTOMAN REIS KAWASAKI YAMAHA SCARA CLOOS
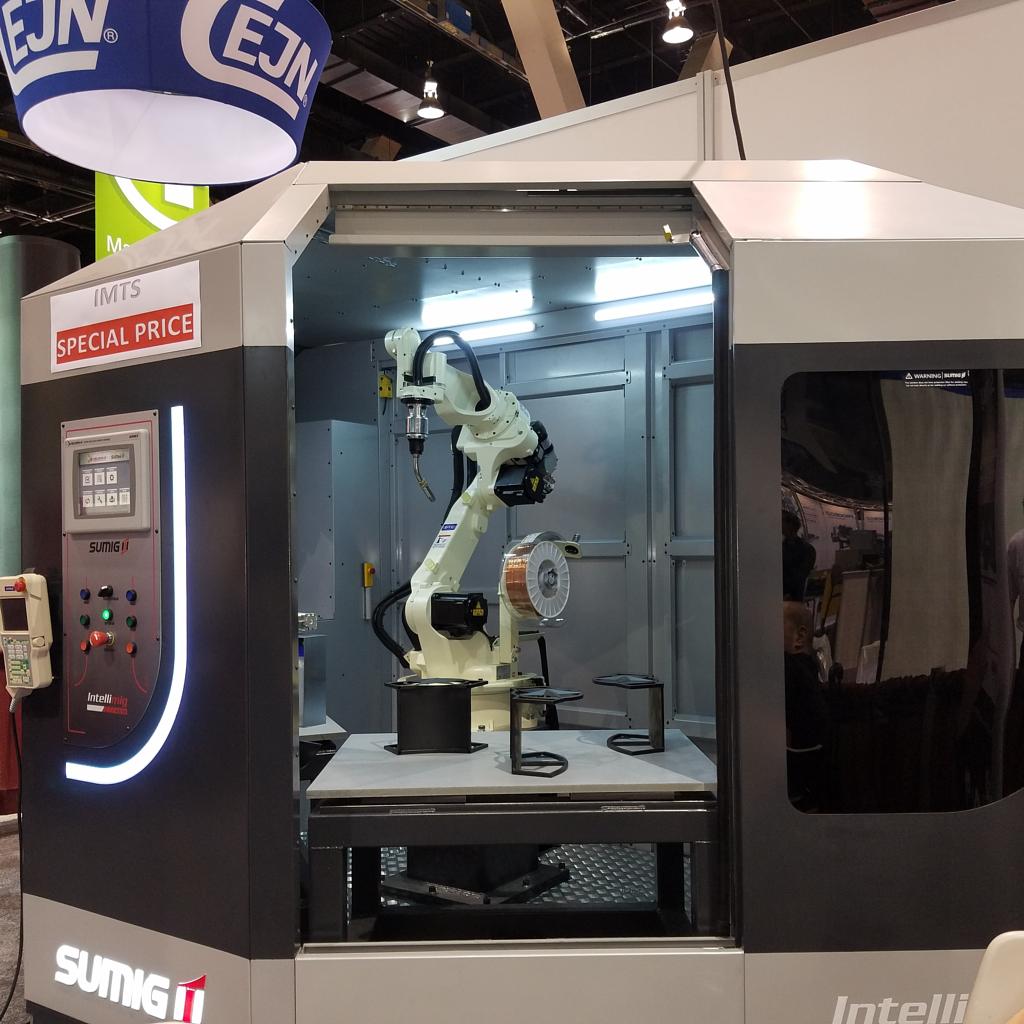
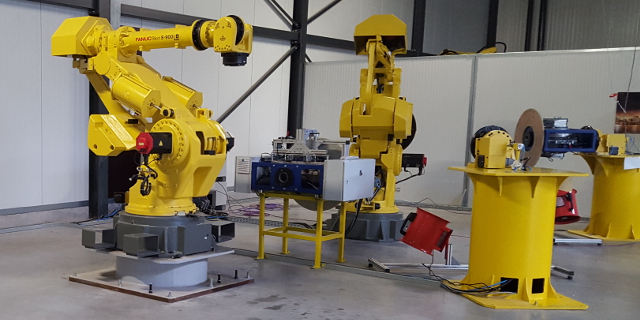
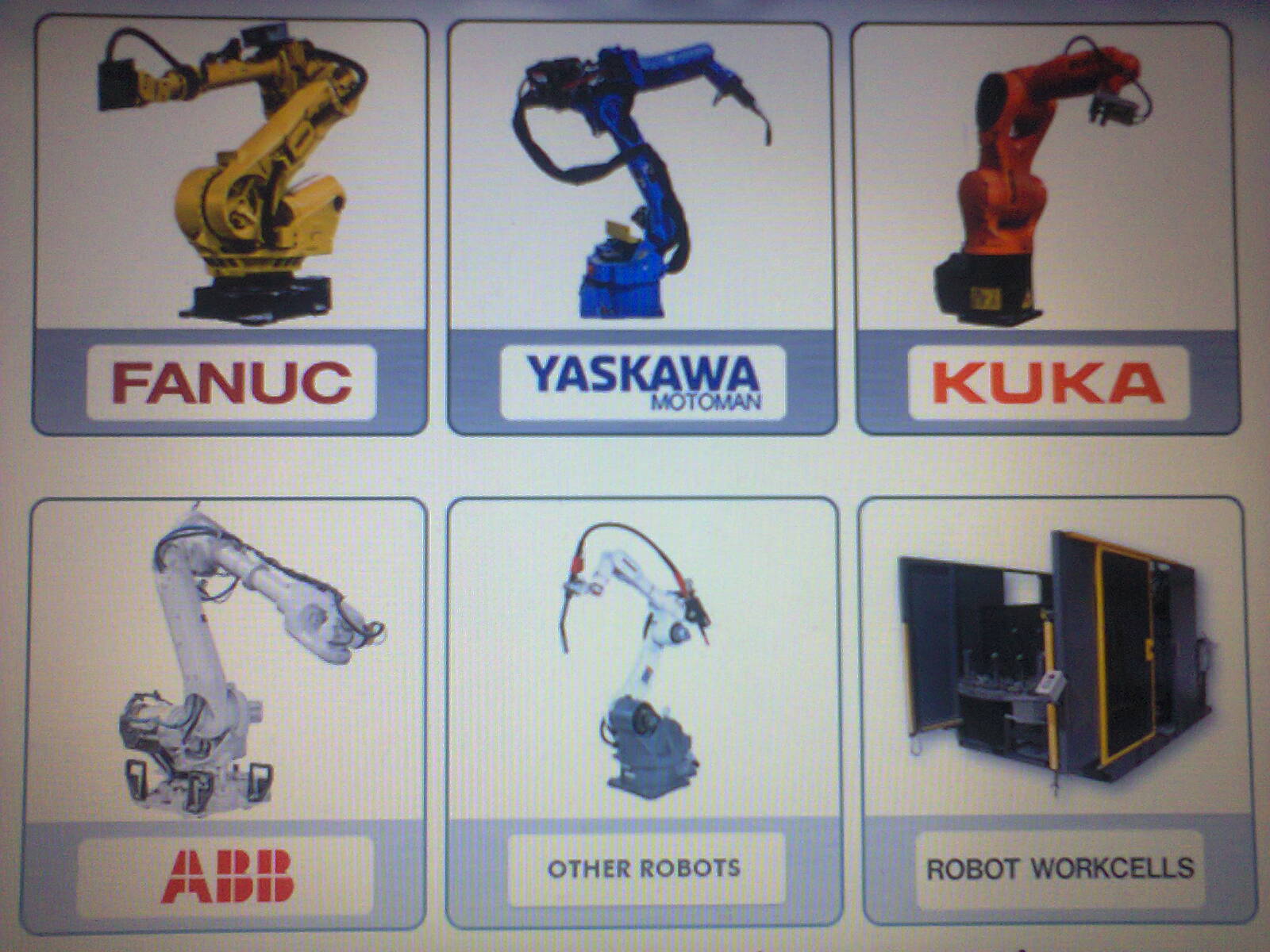
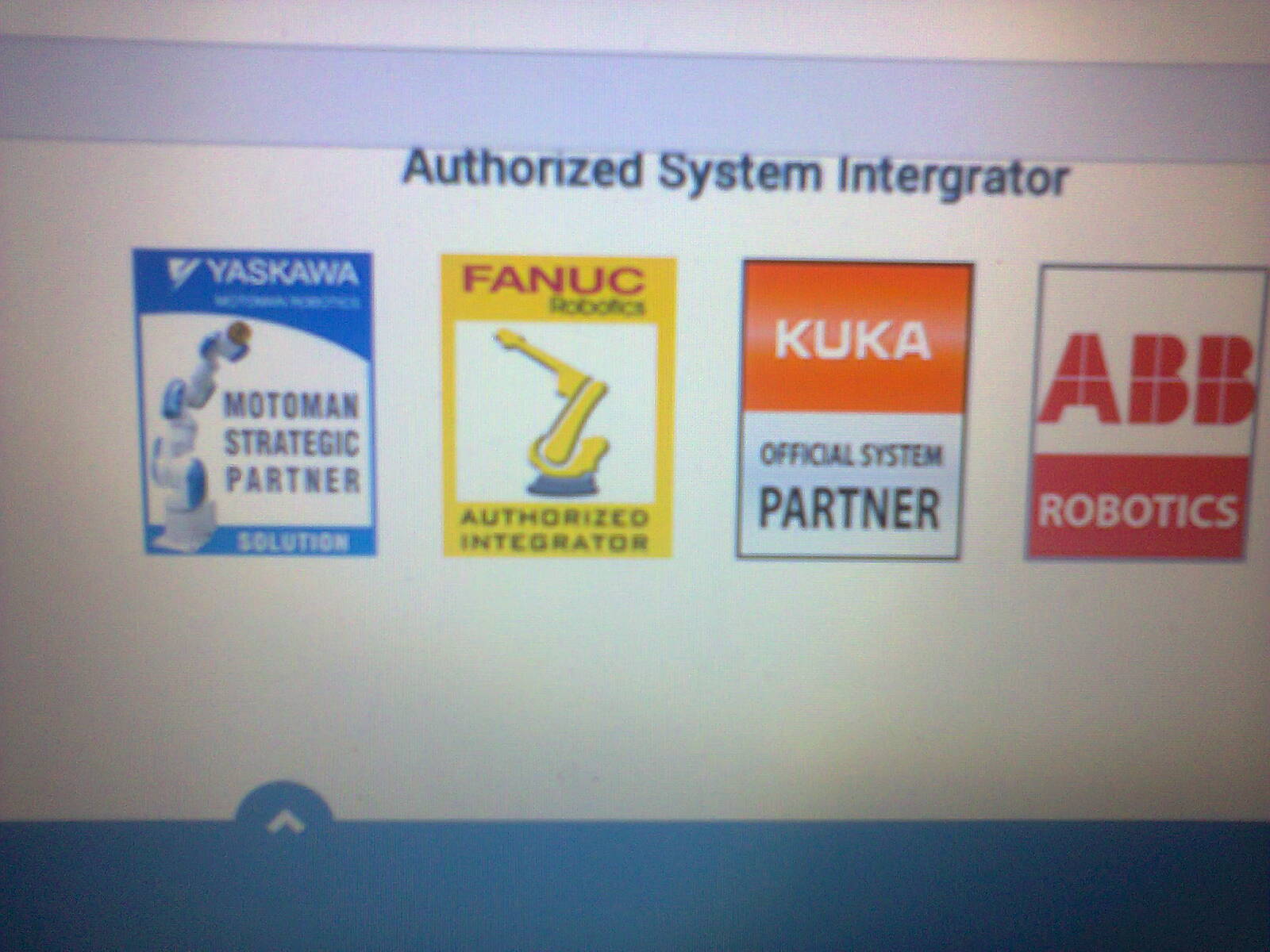
We are specialized in providing comprehensive services in the field of industrial automation from planning to putting into operation. We can provide design and product design, to provide services in the basic offer, as well as tailored solutions, based on customer requirements. We offer our services in planning, mechanical and electrical design, simulation, off-line programming, PLC programming.
ARC/SPOT/FRONIUSCO2/SHIELDED
/MIG/MAG/TIG
BONDING RIVETING FOLDING PRESSING CUTTING MILLING PALLETISING TRIMMING SEALING ROLLING BENDING HANDLING OF PARTS
Robot Experts
Which robot do you need?
We buy Robots &Exchange
Spare Parts
Used Industrial Robots
KUKA
ABB
Fanuc
Motoman
Kawasaki
Scara
Stud Welding
Assembly of parts
Handling of parts
Parts Loading and unloading
Glueing and coating application
Laser welding Nd-Yag
Machining
Palletising
Press tending
Spot-welding
Arc Welding
Please see bellow fotos fresh offers second hand robots
OUR robots FOR YOU
We offers you a stock of used and reconditioned robots, in constant variation, which can be easily after FREE consultation .
You can search for the used robot in different ways by manufacturer, by application, by scope, etc.
If the industrial robot manufacturer is not a determining factor when choosing the used industrial robot you need, then at the time of choosing the most suitable used industrial robot to the needs and specifications of each business, it should be clear what is the specific application for which is to be used.
There are specific industrial robots used for painting, which feature a special anti explosion protection, for palletizing, typically 4 axes and the more widespread are those for manipulation. The latter can also be used for palletizing because by having six axes offer more versatility than 4 axes used industrial robots.
There are two determining factors that define the model of used industrial robot to suit your needs, these are the maximum weight to lift, payload and the arm reach of the robot.
As for how to quantify the maximum weight will be lifted, payload, we must consider the weight of the material itself as well as the weight of the gripper or own tool, which is what is located in the robot wrist.
The second criterion to be defined is the scope of the used industrial robot arm considering the distance or working space between the base from the used industrial robot to the charging or collecting part.
It is to note that one of the two above parameters, scope, arm reach or payload, can make the choice falls on a bigger used industrial robot.
We recommend that you let yourself be advised by people who are immersed in the market of used industrial robots in undertaking the final choice of your used industrial robots.
We provide specialized solutions in fastening technology with the application of ALL industrial robots
• Configuration, setting and commissioning of robots,• programming and optimization of robot path with respect to the quality of scanned data and scanning time,• Creation of simulations, visualizations for presentation needs from project preparation stage for repeat and new applications,• cooperation in the installation, commissioning and transfer of robotic automation solutions• Cooperation in diagnosing faults and removing the robotic automation solutions• training and development of relevant documentation for robotic automation solutions.
Manufacturer brands more widespread in the global market of industrial robots are:
KUKA, STAUBLI, FANUC, REIS, MOTOMAN, ABB, ADEPT, CENCORP, Codiani, COMAU, DENSO, EPSON, EXECHON, JOT AUTOMATION, KAWASAKI, MITSUBISHI, Purple, PANASONIC, REIS, TOSHIBA, UNIVERSAL ROBOTS, YAMAHA, YASKAWA
Offline robot programming
OCTOUPUZ STUDIO
- Process 3D Simulate Commissioning
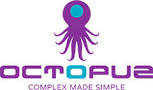
We are EXPERTS who
specialized in trading with used and preowned industrial robots. We don't focus on just one manufacturer and we always work with major brands in the market, such as COMAU ,ABB, KUKA, Fanuc, Yaskawa Motoman and Kawasaki among others.
Industrial second-hand robots
- hen selecting our industrial second-hand robots, we seek the best options, which are better adapted to the most common applications: spot welding, arc welding, palletizing, handling, food sector, pharmaceuticals, etc.
The best used industrial robotsThe aim is to provide the best used industrial robots, so our customers may introduce them in any production process that requires them. Therefore batchs of industrial robots are acquired from large plants, thus, at a lower cost, selecting those which have had a better maintenanance
Robots in perfect working condition
dedicated to the integration of robots in production processes, supplies used robots in perfect working condition. However, many of our clients are robotic systems integrators, allowing us to be able to contact customers with the Integrator that best suits your needs
Technical specialists with high qualifications We have technical specialists with high qualifications and a great experience in the sector of industrial robotics, which make us provide all our used and second hand robots with a 6 month warranty in spare parts.
The sale of your used industrial robots Besides, Our Robots is the ideal solution for the sale of your used industrial robots, as our stock in permanently changing, we will always be willing to consider your proposals.
Commitment to our customers begins even before they contact us
Depending on the application and task, a range of different requirements must be taken into consideration when connecting and integrating robots into machine tools. Perhaps the most common application is when existing machine tools are complemented with robots or existing robot cells are expanded using CNC machines.
The challenge lies in the fact that material-handling robots and machine tools are designed for separate applications by their manufacturers. If they are to work together, they must be connected in the field. It sounds easy, but the two control systems - CNC control and robot control systems - are already engineered, meaning that they speak their own language. As a result, communication between the control systems - and therefore synchronization of the two machines within the production process - must take place via interfaces. It is important that these interfaces be designed in such a way that even external systems integrators, such as machine distributors, can connect the handling robots and machine tools without affecting the applications of the machine tools and robots
The idea of using a PLC-based system rather than a Distributed Control Systems (DCS) has become a philosophical and technical debate in the industry. Distributed Control Systems (DCS) have been the primary solution for process automation but now many PLC vendors are pursuing these applications arguing that a single integrated architecture based on PLCs and/or PACs (Programmable Automation Controllers) is the best approach to total plant automation. In turn, there are DCS vendors that have introduced PLC and PAC products as offerings. The primary logic offered for using a single PLC-based system rather than a DCS for process functions along with PLCs for discrete functions is to have one control architecture for the entire plant. The premise is this offers the best of both worlds. In this article the term PLC will include PAC. Process Plant Control The majority of process plants today have both DCSs and PLCs installed for controls. The DCSs generally control and manage the core processes (food, pharmaceutical, refining, etc.). PLCs are used to control non-core process functions including material handling, water treatment, motor controls, balance of plant operations, air compressor controls, packaging, and other functions. There are plants where PLCs or DCSs control all of the plant functions but at this point these are the exceptions. DCS DCS systems have for many years provided multi-disciplined controllers for logic, sequential and process control, HMIs, custom applications, and business integration on one platform. PLC Although PLCs have become more powerful, they are still based on "loose" component architectures allowing functions to be easily added with hardware and software. For example, a historian may be added to many PLC products by plugging a module into the backplane that acquires data from the controllers, but history communications is done over a separate Ethernet connection. Configuration vs. Programming The DCS from its inception has been designed for configuration as opposed to PLCs which started with a general programming model. DCS configuration uses standard control objects that are automatically linked to the appropriate faceplate, simplifying configuration and leading to standardization. When configuring a tag, everything required is there to connect it to a field point and apply alarm logic, history, version control and other functions, saving time and improving quality. For example, if you have a two input, one output valve, there is a function block library so you don't have to create the logic from scratch. PLC suppliers have been developing new configuration software to provide this level of integration. Technology Levels the Playing Field Today with open technologies, DCS systems are competitively priced with PLCs. Ten years ago there was a marked difference in the cost of technologies used in DCS controllers and PLCs but with processors, memory, embedded software, and communications commoditization, this has become insignificant for new offerings from all vendors. The everyday use of our smart phones, iPads, and electronic games decreases the cost of increased computing power. This is driven by increased unit volume production of processors and related components. Consider that mobile phone shipments in 2010 were 1.39 billion, up 18.5% from the 1.17 billion units shipped in 2009. Enterprise IntegrationIntegration with the enterprise is becoming very important to improve operations and maximize asset management.DCS systems have tied into the enterprise for years, conforming to the Purdue Model and more recently the ISA95 standard. This level of sophistication came later for discrete PLC applications. Virtually all DCS and PLC manufacturers' software is based on Microsoft technologies with standard software interfaces to business enterprise systems for information interchange and synchronized operations. Asset Management Asset management is becoming more important and PLCs are playing catch up with DCSs to provide integrated software for a full range of devices and asset management standards. APC Advanced Process Control Process optimization is another area where traditional PLCs may be lacking when compared to a DCS, which will typically offer a number of tools for optimizing control loops and more advanced alternatives to improve performance of PID control. PLCs are adding these functions with their push into process control. Total Production Optimization Real-time software modeling and control optimization is an emerging function being provided to achieve higher efficiencies by DCS suppliers. This level of optimization is high level, multivariable control based on real-time business management goals, actual feedstock information, production demand, and energy costs - all in an effort to optimize plant profits. Accomplishing this with PLC-based systems at this time can be approximated with loosely coupled software add-ons. Skid & Packaged Systems PLCs on skid mounted and packaged systems for process plants are creating control and automation problems. Skid mounted and packaged systems are factory built units that provide a specific function needed in a plant. The controls and automation on a skid become part of the plant just as much as site installed controls and automation. The dilemma is that many skid vendors have typically standardized on one brand and model of PLC controller and the plant is using another vendor. Ideally the plant process control system has efficient and cost effective multiprotocol interfaces for all PLC protocols. These interfaced subsystems generally require more field engineering to configure and maintain than the other plant controls. Sensor/Control Network Communications The need to connect to multiple industrial networks is a necessity and virtually all process plants utilize multiple discrete and process industrial networks including DeviceNet, Profibus, PROFINET, EtherNet/IP, Modbus TCP, HART, and Foundation Fieldbus. DCSs have highly refined and integrated interfaces to Foundation Fieldbus and HART and adequate interfaces to other industrial automation networks. PLC systems tend to have less refined interfaces to Foundation Fieldbus and HART. In many cases they rely on third party hardware and software with configuration being more labor intensive. Oddly the discrete network interfaces can be an issue with PLC systems since there are many standards and larger vendors optimize the interface and software configuration to their flagship protocols and have weak interfaces to competitive protocols. These other protocol interfaces are typically accomplished with third party interfaces where the software configuration is more cumbersome. DCS Backbone Network DCS backbone networks are typically standard Ethernet hardware but use their own closed,high-performance protocols and natively support redundancy. In DCS systems, the process networks (Foundation Fieldbus, HART) and PLC-oriented networks (DeviceNet, Profibus, Modbus, etc.) are connected to controllers, which are connected to the process DCS backbone. PLC systems use open published protocols that are designed to cover a wide range of applications including simple discrete, synchronized motion control, motor control, and process. Many process control systems require redundancy for I/O, controllers, networks, and HMI servers at various levels. The level of controller redundancy for higher level process applications is new to PLC suppliers and they continue to add options for redundancy. DCS systems generally have easier to apply redundancy solutions but the open networking standard groups such as ODVA and PI International have defined solutions for their protocols particularly with the initiatives for networked machine safety. An advantage often cited by PLC vendors is that all control functions can connect to one Ethernet backbone (process control, discrete, motion control, safety; etc.) In my opinion, this is not a rational engineering approach when configuring plant systems for performance and reliability.Thoughts & ObservationsNew ArchitectureIt sure looks like the PLC vendors who advocate a single control architecture for process plants are essentially creating a DCS system built around their hardware and software components. These PLC vendors are continually demonstrating how their software is like a DCS. In an interview early in 2011 with a business manager at a major PLC company who is pursuing the process business, I asked what distinguishes their offering from a DCS. He responded by rephrasing the question, noting the real question should be what distinguishes their PLC-based DCS from other DCS systems. Following this logic, the decision is between the new PLC-based DCS and traditional DCS offerings. As this unfolds, both DCS and PLC suppliers will evolve and we may eventually see a new architecture but in the meantime plants need to continue to operate and improve. Should the goal be a single unified architecture?I suggest, rather than accepting a suppliers definition of a single unified architecture, that you create a definition for your operations. As part of this process you might think about how open architectures have changed the game, providing you with more options and requiring vendors to be more competitive.
Most systems can answer yes to these questions, so you need to quantify these characteristics to make solid decisions. have never understood how engineers that would never buy a new automobile without looking under the hood and taking test drives will buy an automation system based on vendor demonstrations and PowerPoint presentations. Selecting the right system for your operations requires complex analysis, with a number of considerations, based on production processes, in-house capabilities, and other factors. The time and cost of integration is significant over the life of a system and should be examined as part of the analysis. I suggest having your own control engineer(s) configure some control loops, sensors, I/O configuration, HMI screens, and communications - specific to your applications - for each system under consideration. This can be accomplished with a demonstration system provided by vendors, including controller hardware. This investment upfront can save a large amount of money and lost production time over the life of a system. If the vendor tells you this can only be done by taking a training course on their product, don't walk...run away from this supplier. One thing is clear, process users are getting more options to consider.
Basic Definitions DCS
Many agree that the beginning of the DCS started with the introduction of the Honeywell TDC 2000 in 1975. It was the first system to use microprocessors to perform direct digital control of processes as an integrated part of the system. This distributed architecture was revolutionary with digital communication between distributed controllers, workstations and other computing elements. Computer-based process control systems before the TDC 2000 were mainly data collection and alarm systems with controlled done by pneumatic loop controllers and standalone electronic PID controllers.
PLCThe PLC was invented in response to the needs of the American automotive manufacturing industry primarily to replace thousands of relays, cam timers, and drum sequencers. The big advantage was that programmable logic controllers could be reconfigured with software programming rather than rewiring control panels. The automotive industry is still one of the largest users of PLCs.
PACThe term Programmable Automation Controller (PAC) has been used for over eight years with a few companies claiming to have invented the term. The term refers to more powerful controllers, but the term PAC continues to be imprecise with vendors and analysts each having a different spin on the term. A programmable automation controller (PAC) is a compact controller that combines the features and capabilities of a PC-based control system with that of a typical programmable logic controller (PLC). PACs are most often used in industrial settings for process control, data acquisition, remote equipment monitoring, machine vision, and motion control. Additionally, because they function and communicate over popular network interface protocols like TCP/IP, OLE for process control (OPC) and SMTP, PACs are able to transfer data from the machines they control to other machines and components in a networked control system or to application software and databases.